When it comes to masonry wall constructions, cavity trays play an essential role alongside key elements such as cavity barriers and fire stops. They are designed to keep moisture at bay, ensuring that any rain that penetrates the cavity does not reach the inner leaf, thereby reducing the risk of internal damp which can cause serious problems for buildings and occupants alike. But for cavity trays to be effective, it is important to understand how they work, what the installation requirements are, and also when other considerations need to be taken into account when integrating them with products such as cavity barriers and fire stops.
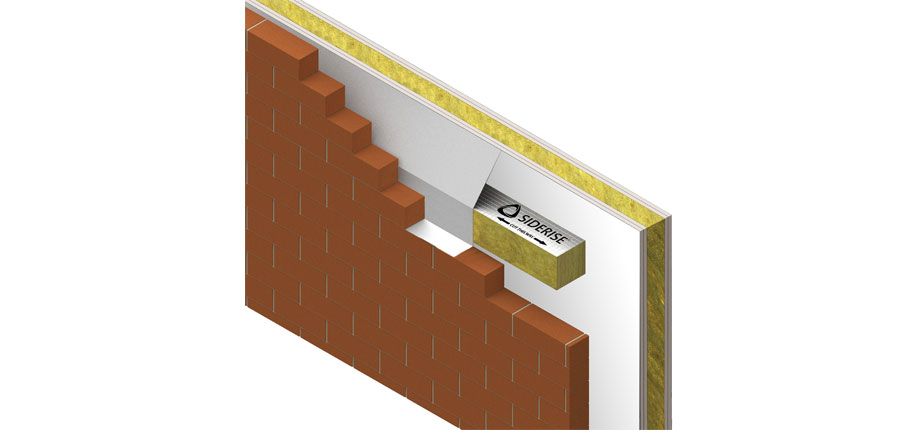
Above: Cavity trays are an important consideration alongside fire stops and cavity barriers.
What is a Cavity Tray?
Cavity trays essentially perform the job of a damp proof course which is angled to bridge the cavity in a way that directs moisture away from the inner leaf and enables it to drain externally. They can be pre-manufactured from a wide range of materials, from heavy plastic to stainless steel and aluminium, to foil faced non-combustible insulation.
When and where should cavity trays be installed?
For solid masonry walls, Approved Document C1 (ADC) to the Building Regulations 2010 – Site preparations and resistance to contaminants and moisture – states that cavity trays should be provided and designed to ensure that water should drain outwards in three different scenarios:
i. Where the downward flow will be interrupted by an obstruction, such as some types of lintel; and
ii. Under openings unless there is a sill and the sill and its joints will form a complete barrier; and
iii. At abutments between walls and roofs.
Although ADC states that this guidance is for solid walls, the same principles apply for cavity walls at any point where the cavity between the external and internal leaf may be bridged, for example by cavity barriers, firestops and cavity closures.
ADC refers to BS 5628-3:2001 for more detailed guidance on alternative approaches to ensuring that precipitation is not carried to the inner leaf. However, this standard has been superseded by the 2005 version, which provides more information on the required configuration for cavity trays, stipulating that they “should step down or slope across the cavity not less than 150mm towards the external leaf and, preferably, terminate in a small drip on the face of the wall”
The Approved Document also provides a detailed map of UK zones for exposure to driving rain (Diagram 12 on page 34), and the minimum cavity widths required to deal with the different levels of exposure for various types of insulated masonry wall construction. These range from 50 to 150mm, indicating the scale of different widths that cavity trays may need to cover, and the need for specifiers to take prevailing weather conditions into account early in the design process.
Installation is key
As with any detailing, not only is it important to get the design right, it is also crucial that cavity trays are installed correctly, or else they will not do the job in hand, and could even contribute to the problem they are designed to prevent. Section 6 of the LABC Warranty Technical Manual2 Version 9 offers detailed guidance on both the design and the installation aspects of cavity trays in 5 different types of external wall construction.
Other considerations
The LABC Warranty Technical Manual highlights the fact that cavity trays should be provided over cavity barriers. The guidance also covers the issue of building movement, which could potentially create problems if cavity trays are unable to accommodate a normal range of movement without loss of integrity.
It is important to note that, for high rise residential and other relevant buildings over 18 metres, there is a requirement for cavity trays to achieve an A1 or A2-s1,d0 Euroclass rating, unless they are between two leaves of masonry (Approved Document B3, regulation 7, paragraph 3a).
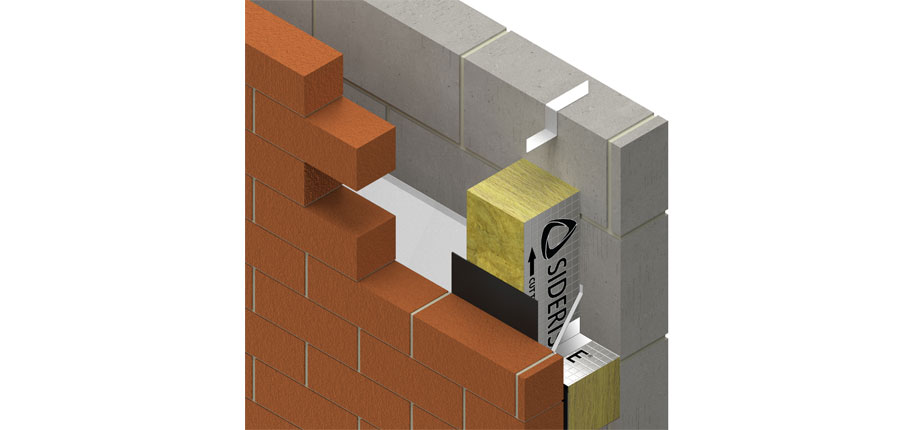
Above: There is ample guidance on how to deal with the requirements, and suitable solutions to meet each of the different challenges.
In short…
With climate change expected to bring increased levels of rainfall to the UK, cavity trays could become an increasingly important part of modern construction, alongside cavity barriers and fire stops. Although at first glance they appear to be straightforward, cavity trays are not a ‘one size fits all’ component. Issues such as cavity size, building movement, and combustibility could all impact the choice of product and ease of installation. Luckily, there is ample guidance on how to assess and deal with these requirements, and meet each of the different challenges that specifiers and contractors face.
For further information, please contact: enquiries@ siderise.com or visit the Siderise website
1 https://assets.publishing.service.gov.uk/government/uploads/system/uploads/attachment_data/file/431943/BR_PDF_AD_C_2013.pdf
2 https://www.labcwarranty.co.uk/media/4222/labc-warranty-technical-manual-v9.pdf
3 https://www.gov.uk/government/publications/fire-safety-approved-document-b
- Log in to post comments