The wide range of innovative products and systems offered by today’s window and door industry may provide housing specifiers with the scope to achieve their performance goals effectively on paper without focusing on the minor components used in their manufacture. However, the reality could be very different.
Reputable window and door manufacturers always have a clear procurement strategy for fasteners, so they know the products they use are fit for purpose. But what are the most important considerations specifiers need to be aware of when it comes to window fasteners?
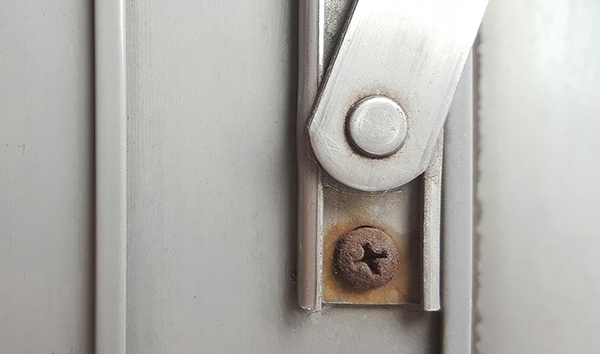
Resistance to corrosion
Any metal component used in the building envelope can be susceptible to the effects of weather and atmospheric conditions, which is why fasteners must be manufactured from metals that can resist long-term exposure to moisture resulting from rain, snow, or condensation.
Rapierstar’s fasteners are available in three different steel alloys: coated carbon steel and two types of stainless steel.
Stainless steel fasteners have historically been regarded as necessary only for windows and doors installed in locations close to the coast due to the saline atmosphere or in busy urban or industrial areas, where localised pollution may be present. Coated carbon steel fasteners are generally regarded as acceptable for most other locations.
However, the reality is far more complex. The ideal type of metal will depend on several other factors, such as the window’s design life and importantly the budget. Of course, the belt-and-braces approach would be for fabricators to use the metal that offers the highest resistance to corrosion for all the windows and doors they produce – austenitic stainless steel – but this is also the most expensive. So, a balance will always need to be achieved.
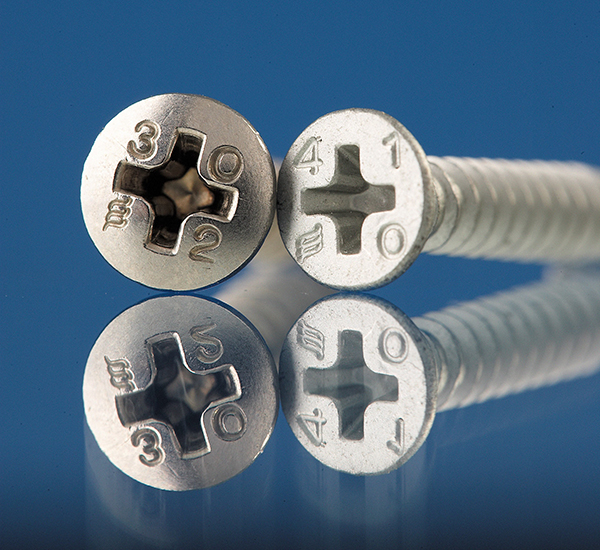
Strength, quality and performance
Like all hardware products, such as handles or locking systems, fasteners must be fit for purpose. Otherwise, the functional operation of windows and doors could result in the need for costly repairs relatively early into their service life. Hence, extensive testing and quality checking of fasteners is crucial throughout their design and manufacture.
Fasteners made to a consistent standard optimise safety and ease of use during assembly. But they must also facilitate strong, secure joints and attachments to ensure the finished window and door will perform to the specification required once installed.
To help achieve this, we conduct a wide range of testing on every batch of fasteners at our state-of-the-art Technical Centre in Cheshire. These include salt spray testing to check that the metal offers the corrosion resistance promised, tests to determine the screw’s ductility and its potential for breakage, the screw’s pull-out strength and insertion speed, and torque testing, which assesses its optimal torsional strength.
Consistent quality through reliability of supply
Every specifier wants consistency in the windows and doors fitted into their housing stock to plan maintenance cycles most effectively and reduce the need for reactive repairs. However, problems associated with the fasteners can result in the need for costly remediation, particularly where the wrong size of fastener is used or one that is unsuitable for the application or framing materials.
Whilst these issues can arise from operatives making the wrong choices due to inadequate training, incorrect fastener use can also stem from supply issues. When stocks of one particular fastener run out during window and door assembly, a substitute fastener that is untested in the assembly may have to be used. That decision could result in quality and performance issues in situ, so window and door manufacturers with reliable fastener supply partners offer another significant advantage.
To learn more about the importance of fasteners in delivering high performing windows and doors visit www.rapierstar.com.
Images © Rapierstar
- Log in to post comments