When designing social housing what are people looking for? High quality at reasonable cost? Speed of construction? Outstanding thermal performance? And, not least, impeccable environmental credentials? The list of wants can be quite daunting but is completely achievable.
More and more designers, specifiers and building contractors are incorporating JJI-Joists into their designs as JJI-Joists tick all of these boxes – and more.
JJI-Joists, from James Jones & Sons Ltd, were the first timber I-Joist to be manufactured in the UK, entering the market in 1999. Since then, as timber I-Joists have gained in popularity, the JJI-Joist has become the clear market leader, with an estimated 45% market share.
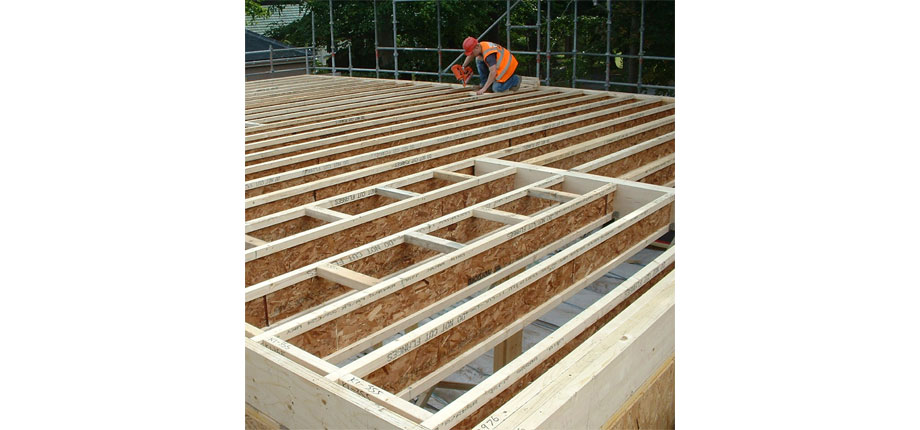
Why use JJI-Joists?
So, what is it that makes them so popular? As with all timber i-Joists JJIs offer a lighter, stronger alternative to traditional timber joists. Their engineered construction, with solid timber flanges and an OSB web make them more stable and less inclined to the warping and shrinkage found with solid timber.
Not just for floors…
But, more recently, JJI-Joists are being used in more than just flooring. Increasing designers are turning to JJI-Joists for wall sections too. Architects appreciate their versatility, and in particular the ability to build highly insulated wall sections. A typical example would be the award-winning Lilac Project in Leeds, by Bristol-based White Design The building incorporates the patented Modcell straw bale wall sections, using JJI-Joists as the structural element of the wall cassettes which help create a highly thermally efficient envelope, with residents seeing annual heating bills of less than £200 a year.
The 9mm OSB web reduces the problem of cold bridging and allows the wall section to be filled with the chosen insulation material – whether it’s straw, wood fibre, Rockwool or the more traditional foam insulation. Using a thicker wall section can allow the building to achieve very high U values with highly efficient, yet simple and easily built structures, whether in pre-fabricated offsite panels or more traditional stick build.
Even more popular is the use of JJI-Joists in roof sections where pre-fabricated cassettes can mean that a building can have a highly insulated roof fully in place in a matter of hours rather than the weeks taken with more traditional building methods
Market leading environmental credentials
JJI-Joists meet both FSC and PEFC certification requirements and can be supplied to either standard. The Forres manufacturing plant is also ISO 14001 compliant. Uniquely, JJI-Joists are accredited to PAS 2050 carbon accounting standards, meaning that James Jones have been rigorously audited and are able to supply an embodied C02E figure for every pack of JJI-Joists sold. A typical 3 bed detached house would, for example have around 395kg of embodied carbon within the floor sets alone. This ability to supply accurate carbon numbers is invaluable for those people looking to create exemplar buildings with a clearly identified carbon footprint.
A story of continual investment and improvement
In the past five years James Jones and Sons has invested almost £15Million in new and improved production facilities and now has the most advanced I-Joist manufacturing plant in Europe, if not the world ensuring flexible manufacturing and guaranteed continuity of supply. The UK-wide JJI-Joist distributor network is now fully geared up with the all new JJI-Joist bespoke software package, JJI Design, meaning that customers are able to have their designs optimised more efficiently and cost effectively than ever before.
For more information please visit the James Jones website
- Log in to post comments