Increasing pressure on contractors to deliver bigger, quicker and cheaper builds can result in mistakes that can sometimes cost lives. The construction industry shoulders much responsibility, so the importance of making fundamental changes to methods of working is immeasurable. Glyn Coates from Zeroignition looks at the flaws in traditional methods of construction – and the solutions offered by adopting an off-site approach, particularly when concerning fire protection.
Select the right contractor
A finished building should be fully compliant and fit-for-purpose. To accomplish this it is essential projects are designed, specified and constructed by accredited professionals. However, it appears in practice that many contracts are awarded to the lowest bidder rather than to well researched and vetted companies.
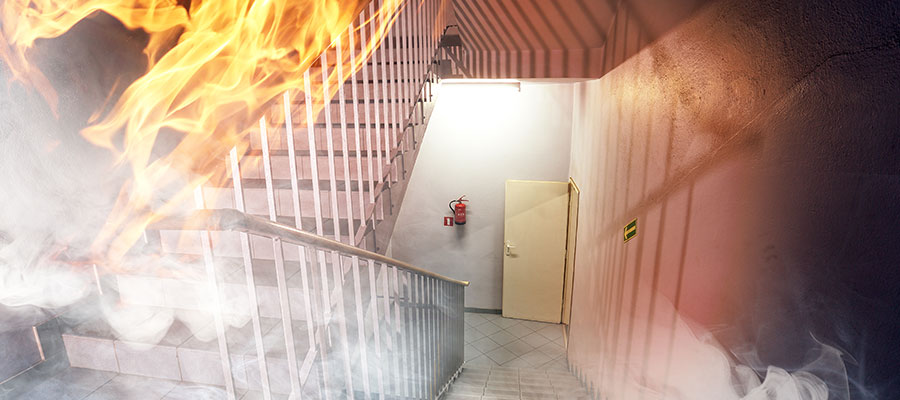
More than the minimum
Generally, product specification stems from the required performance and suitable qualification in relation to BS/EN or ISO testing. But who monitors this and how can we be certain a building meets the architect’s or designer’s performance specification?
While it’s the specifier who completes the list of products required for a project, it’s the contractor who has the license to use inferior products to cut costs. This is a major issue that should be abolished.
Material substitutions chosen to reduce cost should never be considered if safety is compromised. The global construction industry needs to make a change to the way projects are thought about from the early design stages. One change would be to introduce third-party material accreditations from a body like the BBA, rather than relying on manufacturers to self-certify.
The impact of failing to follow specifications
Following Grenfell, it was reported that the intumescent cavity closers, installed as part of the external elevation, were the wrong way around. This mistake throws into question how the error arose in the first place.
Clearly there’s a problem in the industry regarding insufficient policing of what’s being installed and how it’s being done.
Liability dodging, cost cutting and lack of organisation in the chain of command are the biggest challenges our industry is ignoring.
If fire protection knowledge falls short, standards do too
There’s a lack of understanding of fire control and requirements to reach minimum standards. Few know the differences between reaction to, and resistance to, fire or understand that specifying a Euroclass A.1 does not mean it will achieve a 60-minute performance. More education is needed.
Currently fire protection considerations lack the priority they deserve. Rather than an after-thought near the end of the process, they should be thought of as an essential building foundation and built into initial designs and within products.
Industry interrogation
Two parts of the build program require immediate attention.
First, the overall design, in particular ensuring the priced project with the ‘equal and approved’ reference meets the performance requirement on all levels, especially against fire.
Second, the necessity to supervise and police the construction program so the right products are installed and maintained in the correct way by qualified contractors.
It’s a huge task for a reactionary industry. The situation could be improved with a few simple alterations. Greater levels of control are needed across:
- Materials – ensuring they’re part of an umbrella accreditation and testing system.
- Cost – this shouldn’t come first.
- Quality control – there needs to be a clear chain of authority on builds to ensure there is a central role overseeing products, installation and construction methods.
- Traceability – all components in fabricated systems need to be marked and logged to ensure if the worst happens, sub-contractors and manufacturers are held accountable.
- Flexibility in design – architects and clients need a greater understanding of the costs and limitations of materials to reduce specification errors.
Looking to the future
Offsite manufacturing seems to be heading in the right direction. Expanding this into all construction market sectors is possible, but measures need to be taken so that quality control over components being manufactured develops ahead of the game. Clients and specifiers need peace of mind when buying.
The lowest cost shouldn’t be the first consideration. Cost-effectiveness is important but shouldn’t take precedence over building safety, quality or performance. Research and due diligence are key to helping to improve standards. So is refusing to work with sub-quality contractors and manufacturers.
We know what needs to be done. Drawing inspiration from MMC and similar industries, particularly where manufacturing and installation is present, means that we can translate the same high standards and way of working to move away from being driven by cost, to being driven by quality and safety. Let’s go back to basics and change the foundations of how we work.
For more information on MMC and fire protection see the Zeroignition website.
- Log in to post comments