“Ever since the Grenfell tragedy, a lot of areas need to be addressed and revised”, says Lee Caulfield Director of UK Sales at Titon Ventilation Systems. Lee stresses that even though procedures are in place, the current regulations need to be changed.
Lee continues “In the aftermath of recent tragic, fire-related events, it has become apparent that various products within a building’s make-up need to be non-combustible”.
Air Bricks are primarily used for ventilation; passively or mechanical depending on the application. Traditional materials used include clay, cast iron and plastic, with plastic being the preferred option.
The aim of the passive air brick is to allow air to flow through into a building to help reduce humidity, clearing the stagnant air and keeping the area cool. A mechanical air brick or terminal will be used to assist the flow of air via ducting in and out of a building if used within a mechanical ventilation heat recovery system (MVHR), or extract if a central mechanical extract systems (MEV).
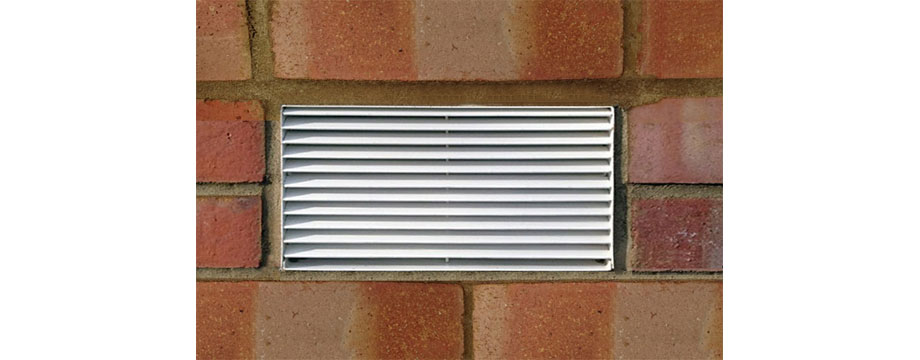
When looking at current legislation, it can be seen that air bricks located above 18 metres need to be non-combustible and help restrict any fire that may progress on the outside of a building.
Approved Document Part B (ADB) states ‘Materials which become part of an external wall, or specified attachment, of a relevant building are of European Classification A2-s1, d0 or A1, classified in accordance with BS EN 13501-1:2007+A1:2009’. Therefore, if a building is above the 18 metres threshold then all air bricks must meet classification A2-s1, d0 or A1.
There was discussion about changing the legislation from 18 metres to 11 metres for non-combustible products, but this only changed for sprinklers and signage in May 2020.
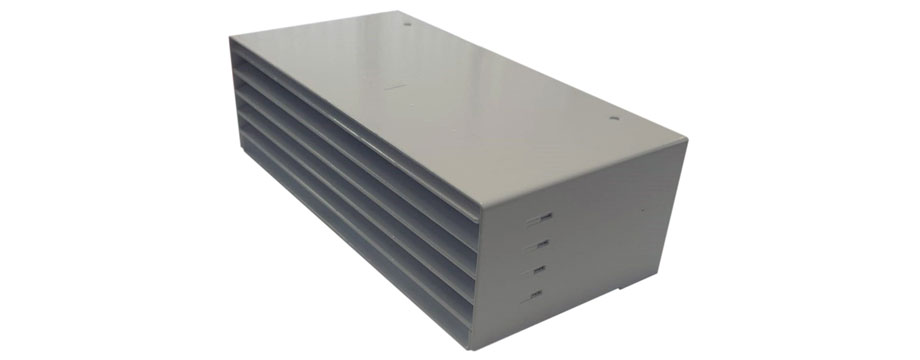
Air bricks in mechanical ventilation systems can use plastic air bricks below 18 metres - this has been done for a number of years. It is legal, but as stated, needs to be addressed as these air bricks are combustible. Table 1 demonstrates the difference between a plastic air brick (Grade E) to a metal air brick (Grade A1/A2). Lee continues ”you can see the difference between the two, the safety aspect is massive, yet the Government have failed to address this’”.
From table 1, it can be seen that even though plastic air bricks are legal to be placed into a building below 18 metres, this does not hide the fact that they can contribute to fire and are a fire major hazard.
The Fire Protection Association (FPA) demonstrated how quickly one of these vents (plastic air brick) can catch fire using nothing more than a cigarette lighter. In a fire test the plastic air brick was alight in 3-5 seconds, with the flames moving inwards and causing a large fire on the timber frame*.
Titon have produced a superior metal air brick to help remove the dangers given by plastic air bricks in mechanical ventilation systems. The Titon FireSafe® Air Brick is the only air brick tested to BS EN13141-2:2010 to quantify its performance for a ventilation system.
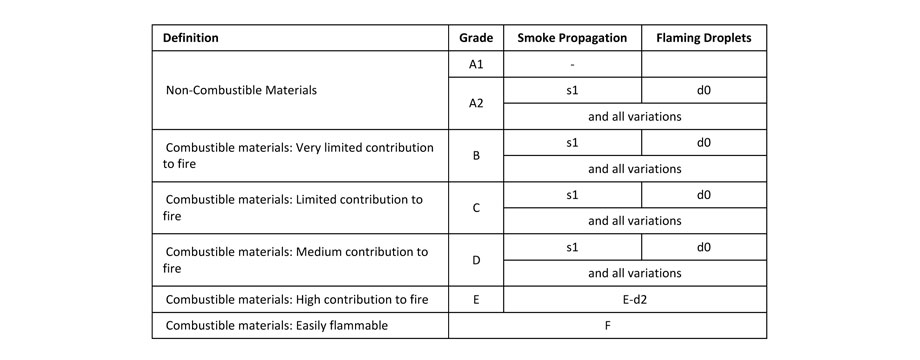
Lee concludes “Fire Safety in the wake of Grenfell is paramount and it is to the responsibility of forward thinking manufacturers to take such products into consideration. It would be expected in future that ADB will change and evolve to cover up gaps that it has, but until then, manufacturers like Titon must develop and educate the market place for the benefits of fire safety”.
If you would like more information, please go to www.titon.com/firesafe
- Log in to post comments