A brand new residential development in Manchester is meeting its environmental planning requirements thanks to an Ecodan system providing community heating to 105 new homes.
The Aaben is a modern development of 105 homes, all available for market rent, on Leaf Street in Hulme. Located just south of Manchester’s city centre, Hulme boasts a creative art scene, independent restaurants and cafes and a thriving local community.
The development itself is named after an old building dating back to the 1920s which was situated close by until it was knocked down in 1993. For decades before it had served as a community cinema and, for a short time, a bingo hall.
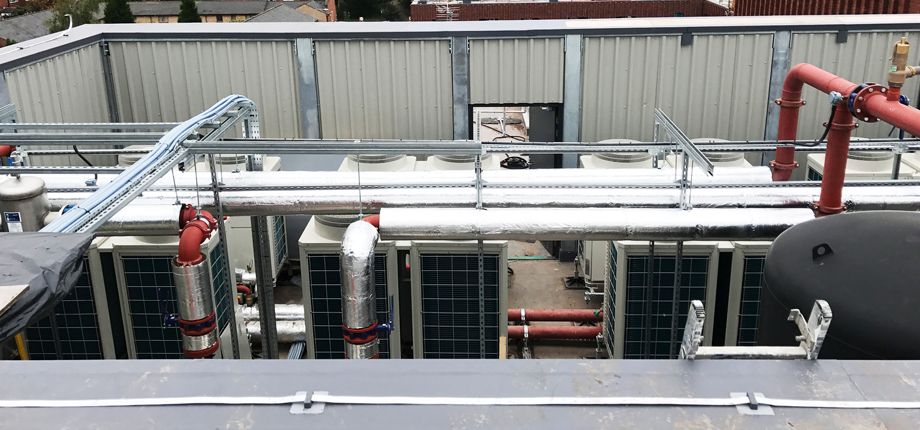
The new Aaben is a mixture of 1, 2 and 3-bedroom apartments set around communal, external space, and 3-bedroom town houses with private gardens. Many of the living rooms benefit from direct sunlight and a shared public garden sits at the centre of the development for the wider community to enjoy.
Designed with quality, comfort and energy efficiency in mind, the homes include a range of features that will benefit the environment and reduce residents’ energy bills.
The original design was based on a ground source heat pump (GSHP) but the cost proved beyond the required budget, so design consultant Engineering Design Partnership (EDP) was tasked with value engineering the scheme.
This led to Mitsubishi Electric’s involvement, as Dan Martell, Design Engineer at EDP, explained: “Following the successful installation of a Mitsubishi Electric air source heat pump (ASHP) system on a previous residential scheme we recommended the Ecodan ASHP system as we felt it would be a well performing, cost-efficient solution ideal for The Aaben.”
One of the key features included in the design was the use of a heat pump system in order to achieve strict carbon reduction targets (more than 35% above Standard Assessment Procedure) to gain planning permission.
Building work began in November 2016 and Proline Mechanical was the installation company assigned to the project.
Proline is one of the UK’s leading building services engineering and maintenance contractors specialising in detailed revit design, thermal dynamic modelling, BIM, engineering installation and commissioning of mechanical and electrical services.
Proline installed a multiple unit Ecodan system on the main roof of the development. Consisting of 8 x CAHV-P500YA units, the community heating system provides hot water to a heat interface unit located within each dwelling for hot water and heating within that dwelling. Each tenant is charged accordingly via a heat meter measuring how much heat energy is taken from the network.
Proline’s Project Manager, Paul Gledhill, said: “The Ecodan system was perfect for this project as the ASHP units are designed to meet the heating and domestic hot water (DHW) requirements for all dwellings via a district heating system. As the system is located on the main roof very near to dwellings there were some sound issues to overcome but these were easily resolved with the erection of an acoustic wall to prevent sound breaching the plant area.”
The ASHP system boasts a capacity of 344KW and can operate at sufficiently high temperature to provide heating and DHW, and a 6,000 litre buffer enables the system to store energy for short peak demand periods.
The Aaben was completed in the autumn of 2017 and thanks to the Ecodan system is eligible to benefit from the non-domestic Renewable Heat Incentive (RHI).
8 x CAHV-P500YA Monobloc Air Source Heat Pump Units providing individual heating and hot water to 105 apartments
Industry-leading technology guarantees performance down to -10ºC
The system utilises a 6,000 litre buffer tank to store thermal energy for short peak demands Each apartment has a localised heat interface unit and heat meter to allow for individual billing.
“Air source heat pumps are being used more and more by social housing providers who have realised how they can help reduce fuel poverty whilst also ensuring better protection for the HAs assets and an improved CSR profile,” explained Sharon Oliver, marketing manager for the Ecodan range of heat pumps.
“In the main, this has usually been with the use of individual units serving individual properties, but this development at Leaf Street, Manchester shows the full potential that heat pumps can offer in providing reliable, controllable community heating.”
The project uses the Ecodan CAHV outdoor compressor which on its own has a capacity of 42kW. Where the system offers such potential for community heating though is its ability to form part of a multiple system of up to 688kW capacity.
This allows the overall system to cascade the available units on and off to meet the load from a building, or a community. As an example, a 16 unit system allows 0.5kW increments of capacity, from 18kW all the way up to 688kW.
This level of modulation is unprecedented within the heating industry and the Ecodan CAHV also comes with cascade and rotation built in to help prolong the life of the equipment.
“We’ve had a lot of interest in this as the system can deliver renewable heating to a whole community,” explains Sharon Oliver. “In addition to this though, as shown in the case of Leaf Street, all of the individual apartments still retain individual control and individual billing.”
The Ecodan CAHV units can provide from 25°C up to 70°C water flow temperatures without booster heaters and will deliver 43kW per unit at -3°C, with minimal drop off down to -20°C.
- Log in to post comments