There is no doubt that the need to build more houses has become one of the key issues for all political parties and it is great news to see both government and opposition expressing determination to increase the number of affordable and rented homes. The challenge, of course, is how to actually build them.
For the past two years, H+H has been working with SIG to develop an entirely new concept in modern masonry construction: the SIG I-House System incorporating Celcon Elements from H+H. The promise of this innovative new offer is to deliver the complete weatherproof shell of a masonry house on site in just one week.
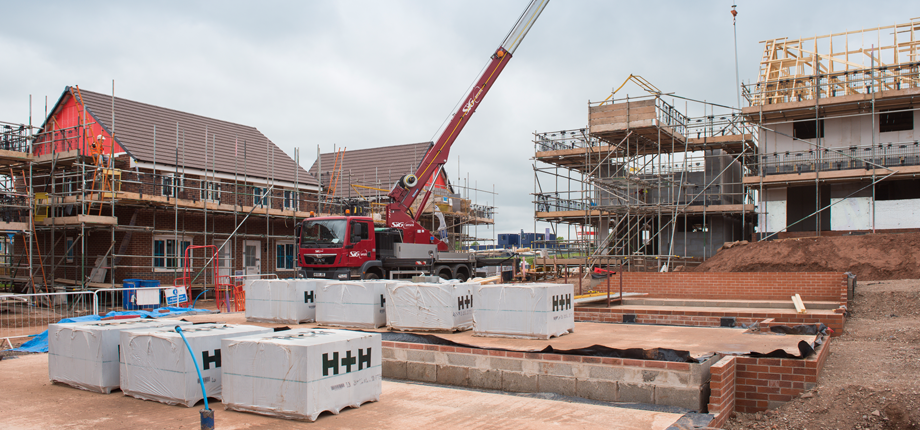
Aircrete has been the material of choice for housebuilders for decades and, as the leading UK manufacturer of aircrete blocks, we at H+H are always keen to point the advantages of traditional masonry construction. The benefits of this robust, thermally efficient and, most important of all, durable material ensure that aircrete has a regular presence on building sites around the UK.
While our Celcon Blocks remain a trusted standard choice for housebuilding, we also recognise that speed is of the essence – particularly when delivering social housing projects where there is a pressing and immediate need to accommodate families who may have been waiting for years.
Successive governments have suggested that the only way to speed up the delivery of new housing is to move to entirely offsite methods but the housebuilding industry has been slow to adopt this approach. It is a conservative sector and the most successful innovations are those which use familiar materials and techniques as the basis for change.
Over the years H+H has introduced a series of innovations to improve the performance and speed of building in masonry. Our Thin-Joint System and Rå House method can deliver a complete masonry shell in dramatically reduced time, compared to a traditional build, but have struggled for widespread adoption largely because they require a change in technique for site workers. Even with H+H providing on-site training and support it has been difficult to introduce any innovation that requires site workers to change their habits.
However, the current market conditions in the UK are perfect for radical thinking and offer an ideal opportunity for H+H to introduce its Celcon Elements. These storey-high panels of aircrete are installed using a crane and a fast-setting thin-joint adhesive, allowing entire walls to be constructed in hours rather than days.
The panels have been used in Europe for decades to produce robust houses at great speed, but we had not found a way to accommodate them into a build process that suited the UK market.
The breakthrough came through collaboration with SIG. Combining Celcon Elements with pre-fabricated timber floor cassettes, a pre-fabricated roof system and insulation for the external walls, all delivered on site by a specially trained and dedicated installation team, gives a complete solution.
Early site trials of the system revealed its success in delivering straightforward housing designs in record speed. Single storey, two storeys or two storeys with room-in-the-roof designs in detached, semi-detached or terraced configurations are equally successful.
Best of all, this new way of working is based on a material that is completely familiar to all the trades people on site – the electricians, plumbers and decorators know how to work with aircrete and time is saved as bricklayers can be working on the brick facades at the same time as the interior trades are working inside the building shell.
Builders looking to work to the old Code 6 of the Code for Sustainable Homes will be reassured to know that houses built using H+H aircrete have been used on Code 6 projects, more recently H+H aircrete has been used on several Passivhaus projects.
The system has been welcomed on site by housebuilders relieved to find a really innovative solution based on a material with which they are entirely familiar and whose performance is not in doubt.
The SIG I-House System has been rigorously tested and the final accreditation that should pave the way for rapid adoption is the Build Offsite Property Assurance Scheme (BOPAS) which was recently awarded to the System. Carried out by Lloyd’s Register, BOPAS is a process evaluation designed to provide reassurance as to the quality, reliability and durability of new methods of building.
Originally targeted at lenders, BOPAS supports one of aircrete’s most important claims – that of longevity. The accreditation includes an expectation of at least a 60 year lifespan for the build and should provide reassurance to asset owners that a new technique can be relied upon for the long term.
Whether the SIG I-House System should be categorised as offsite or traditional is open to question, but the definition is undoubtedly less important than the effect: a masonry house on site in just one week.
- Log in to post comments