The Kingspan TEK Building System is providing a precise offsite building solution for one of the country’s largest Passivhaus developments in Bowthorpe, Norwich.
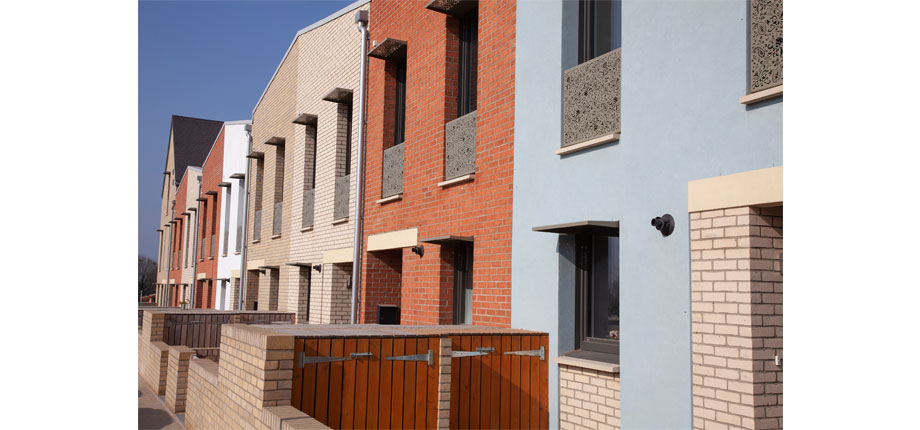
Rayne Park is the first development by Norwich Regeneration Company, wholly owned by Norwich City Council, and will include a mixture of private and affordable housing. RG Carter are constructing 112 of the 172 properties on the development to the Passivhaus Standard. The internationally renowned energy efficiency standard requires buildings to be both highly insulated and airtight.
After reviewing the market offering to achieve the demanding fabric requirements of the Passivhaus Standard, it was concluded that the Kingspan TEK Building System was the best solution for the project on the basis of technical specification and value offered.
Kingspan TEK structural insulated panels (SIPs) feature a high-performance insulation core sandwiched between two layers of OSB/3. The panels were fabricated to the site’s requirements by Kingspan TEK Delivery Partner, Kingspan Timber Solutions. This offsite fabrication process allowed the panels to be factory cut to the specific design requirements, minimising waste and allowing an accurate, fast-track erection process on site.
Kingspan TEK Building System panels can achieve U-values of 0.20 – 0.17 W/m2.K, or better ‘out of the box’. With the addition of an additional layer of insulation, the site team were able to further improve the thermal performance of the external walls – achieving a final external wall U-value as low as 0.09 W/m2.K.
The panels’ proprietary jointing system not only allows continuity of insulation at junctions but, in combination with the OSB/3 facings, also helps to create highly airtight buildings. Once the outer shell was erected, RG Carter installed an additional internal membrane and applied airtight tape to all joints, resulting in a final air leakage rate of from 0.37 to 0.56 air changes per hour @ 50 Pa. This highly airtight design necessitates the use of a mechanical ventilation heat recovery system (MVHR) to maintain a constant supply of fresh air within the properties. MVHR units use the heat from outgoing stale air to warm incoming fresh air, further reducing the property’s heating demand and creating a fresh and comfortable indoor environment.
It is expected that the properties will have a heating demand of just 11 kWh/m2a and a primary energy requirement pf 77 kWh/m2a. This heating demand is around 10% of that of an average home (estimated to be 140 kWh/m2/yr ), making them both cheap to run and comfortable to live in.
- Log in to post comments